智能革新是否真能破解制造业的“效率魔咒”?
当传统制造业还在为人力成本上升、供应链波动和产能过剩发愁时,全球已有企业通过“智能革新赋能未来制造业软件高效驱动全链升级新纪元”的实践,交出了一份惊人的答卷:海尔工厂的智能生产线良品率提升至97%,富士康的机器人调度系统让iPhone主板贴片效率提升12%,富唯智能的复合机器人甚至将人力成本削减了90%。质疑声始终存在:智能化是否只是大企业的“烧钱游戏”?中小厂商如何跨越技术与资金鸿沟?
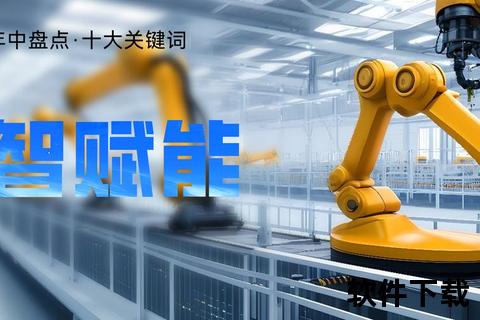
1. 全链智能化:从“单点突破”到“全局优化”
传统制造业的数字化往往停留在设备联网、数据采集等单点环节,而智能革新要求从研发、生产到物流的全链重构。例如,海尔卡奥斯工业大脑通过“大模型+工业机理”融合,实现了从设计仿真到质量检测的全流程覆盖。在冰箱生产线中,其AI视觉系统可识别0.1毫米的焊接缺陷,并通过数字孪生技术提前模拟工艺参数,将产品研发周期缩短30%。
华为的实践则更具代表性:其工业AI质检平台整合了800多个图像处理算法,在汽车零部件检测中,准确率从人工的85%跃升至99.5%,同时将检测时间压缩至毫秒级。这种“软件定义制造”的模式,让产线切换新产品的调试周期从7天降至2小时。
2. 人机协作:效率天花板能否被打破?
智能机器人与人类的关系不再是“替代”,而是“共生”。富唯智能的复合机器人在铝制品加工车间中展现了这种可能:通过3D视觉导航和AI决策系统,机器人可自主规划路径、动态避障,每小时处理铝块数量是人工的3倍,良品率从92%提升至97%。更关键的是,其低代码部署平台让产线调整仅需15分钟,打破了传统自动化设备“刚性固化”的局限。
中国移动的“九天”平台则探索了另一种路径:通过5G+边缘计算,将云端AI能力下沉至工厂终端。在某汽车焊接车间,系统实时分析电流波动数据,提前48小时预警焊枪损耗风险,避免因设备停机导致的每小时50万元损失。
3. 行业know-how:AI如何跨越“经验壁垒”?
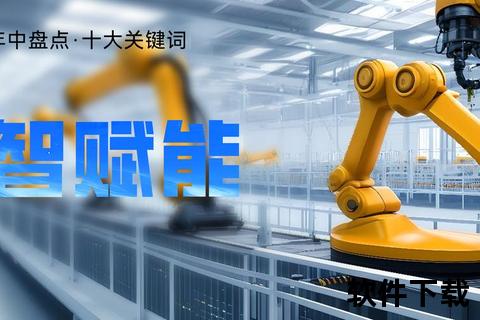
制造业最深的护城河往往是数十年积累的工艺经验,而AI正通过“知识图谱+强化学习”破解这一难题。创新奇智的AInnoGC平台在汽车装备制造中,将老师傅的调试经验转化为2000多个工艺参数模型。例如,在发动机装配环节,AI通过分析历史数据发现:当环境湿度高于70%时,拧紧扭矩需增加0.5N·m,这一微小调整使产品故障率下降18%。
DeepSeek在半导体封装领域的突破更具颠覆性:其强化学习模型协调2000台机器人协同作业,解决了多机路径冲突的世界难题。在富士康的iPhone主板贴片产线中,这种动态调度使日产能突破120万台,且设备能耗降低15%。
迈向智能革新的三大行动指南
1. 分阶段推进:中小企业可优先部署智能质检、预测性维护等“轻量级”应用(如华为AI质检平台),单点投入回报周期控制在6个月内;大型企业则需构建工业互联网平台,打通数据孤岛。
2. 建立数据闭环:从设备实时数据(如振动、温度)到工艺参数(如压力、转速),需通过边缘计算实现毫秒级响应,再结合云端模型持续优化。
3. 生态协同破局:借鉴海尔卡奥斯模式,联合产业链上下游共建知识共享平台,将行业经验转化为可复用的AI模型库。
智能革新赋能未来制造业软件高效驱动全链升级新纪元已不再是概念,而是正在发生的现实。从柔性产线到智慧供应链,从人机协同到知识沉淀,这场变革的终极目标,是让制造业从“经验驱动”跃迁至“数据驱动”,在效率与创新的平衡中重塑全球竞争力。