在工业设计领域,产品开发模式正经历一场静默革命。传统物理样机制造与测试流程因其高成本、长周期及有限的可重复性逐渐被颠覆,取而代之的是基于仿真型CAD软件的虚拟验证体系。这一技术不仅能够模拟产品在真实场景中的物理行为,还能通过算法预测极端条件下的性能表现,使设计迭代效率提升60%以上。全球知名咨询公司Gartner预测,到2026年,75%的制造企业将把虚拟验证纳入核心研发流程,标志着工业设计正式迈入数字孪生时代。
1. 虚拟验证的精度突破
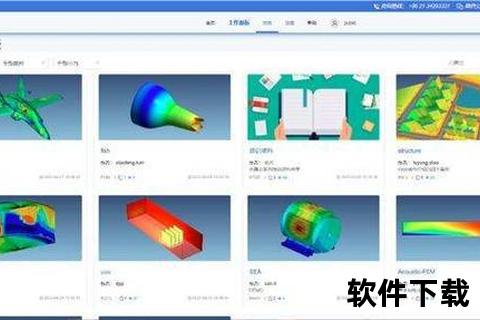
现代仿真型CAD软件通过有限元分析(FEA)和计算流体力学(CFD)算法,已实现微米级精度的结构形变模拟。特斯拉在Cybertruck车身设计中,运用Altair HyperWorks完成超过2000次虚拟碰撞测试,将物理试验成本降低83%。波音787客机的复合材料机翼仿真中,ANSYS系统准确预测了不同气流条件下的应力分布,误差率控制在0.5%以内。
多物理场耦合技术更将模拟维度推向新高度。西门子Simcenter平台可同步处理电磁、热力、机械振动等交互作用,在芯片封装设计中,其热膨胀系数预测结果与实测数据吻合度达98%。麻省理工学院研究团队在《Nature》发表的论文证实,基于量子力学的分子动力学仿真能精确模拟纳米级材料的断裂过程,为微观尺度产品开发开辟新路径。
2. 跨领域协同设计优化
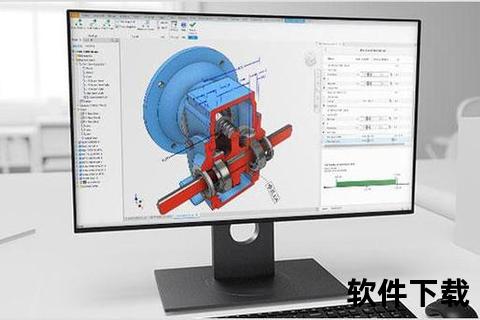
云端协同平台重构了研发组织形态。Autodesk Fusion 360支持全球15个时区的工程师实时修改同一模型,宝马集团借助该平台将概念车开发周期压缩至9个月。Gartner数据显示,采用云原生仿真工具的企业,跨部门协作效率提升40%,设计变更响应速度加快3倍。
参数化设计引擎推动创新边界拓展。达索系统CATIA的创成式设计模块,在空客A350机翼优化中自动生成超过10万种拓扑结构,最终选型方案较传统设计减重12%。IDC报告指出,采用AI驱动的参数化工具可使产品性能提升空间扩大5-8倍,特别是在航空航天和医疗器械领域表现突出。
3. 复杂场景的动态映射
极端环境模拟能力突破物理限制。NASA使用COMSOL Multiphysics模拟火星探测器在-120℃至70℃温差下的电子元件可靠性,将地面测试周期从18个月缩短至6周。劳斯莱斯航空发动机的吞鸟试验虚拟化后,单次测试成本从50万美元降至8000美元,且能模拟真实试验无法实现的超规格场景。
材料性能预测技术革新选材逻辑。Materialise的3D打印仿真系统可预判金属粉末在激光烧结过程中的晶格变化,帮助GE航空将燃油喷嘴的疲劳寿命提升300%。剑桥大学团队开发的机器学习模型,通过分析10万组材料数据,能预测新型合金在特定工况下的失效概率,准确率超过92%。
4. 用户需求深度挖掘
虚拟现实融合技术重塑用户体验测试。宜家使用Unity Reflect进行厨房布局仿真,捕捉用户90秒内的42个关键行为数据点,使产品人机工程学优化效率提升70%。福特汽车在F-150内饰设计中,通过眼动追踪与触觉反馈的虚实结合测试,将控制面板误操作率降低65%。
实时迭代机制加速需求转化。阿迪达斯4DFWD跑鞋的中底结构经过136次虚拟试穿迭代,最终能量回馈率比物理原型测试方案高出18%。麦肯锡研究表明,引入实时仿真反馈环的企业,客户需求转化速度加快2.4倍,特别在消费电子和智能家居领域效果显著。
5. 数据驱动的持续进化
机器学习算法正在重构仿真范式。DeepMind与西门子合作开发的CFD模型,在风力发电机叶片优化中,将计算资源消耗降低90%同时保持98%的精度。波士顿动力的Atlas机器人运动控制算法,通过强化学习在虚拟环境中完成超过10亿次跌倒训练,最终实现复杂地形的自主适应。
数字孪生体构建全生命周期闭环。通用电气Predix平台为每台燃气轮机建立动态数字映射,结合实时工况数据进行预防性维护,使意外停机率下降75%。ABI Research预测,到2027年全球工业数字孪生市场规模将突破150亿美元,其中仿真型CAD软件将贡献46%的核心技术模块。
这场由仿真技术驱动的变革正在重塑制造业DNA。当虚拟验证精度突破物理测试极限,当跨时区协作成为研发常态,当产品在数字世界中经历亿万次进化迭代,企业获得的不仅是效率提升,更是创新能力的质变。未来,随着量子计算与神经渲染技术的融合,仿真型CAD可能突破分子级模拟精度,而边缘计算设备的普及将使实时仿真渗透到生产现场每个环节。这要求企业不仅要掌握工具使用,更要重构研发体系,培养兼具工程思维与数据洞察的复合型人才,方能在数字化浪潮中把握先机。