一、效率提升是否真能突破传统瓶颈?
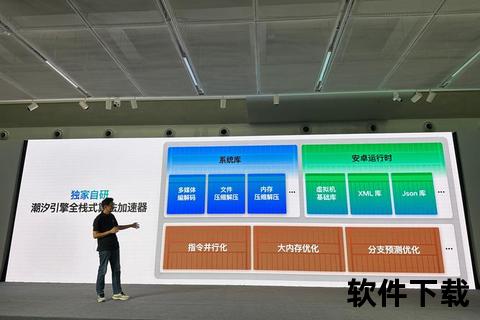
在传统线切割编程中,工程师常需手动调整切割路径、补偿参数和加工顺序,耗时长达数小时甚至数天。某汽车零部件厂商曾反馈,其模具加工周期中,编程环节占比超过30%。智能革新高效能线切割编程软件极速精准升级体验通过算法重构,将这一痛点彻底打破。
以瑞士夏米尔机床用户为例,其引入EdgeCAM的自动切割策略后,通过预设粗加工、精修、料头移除的无人值守流程,单件模具加工时间从8小时压缩至3.5小时,效率提升58%。软件内置的“特征查找”功能,可自动识别实体模型中的3D轮廓与锥度区域,减少人工干预环节达70%。更关键的是,软件支持多料头同步处理,例如在切割带复杂直角形变锥的航空零件时,系统自动生成火花间隙补偿方案,避免传统编程中因参数错位导致的返工问题。
二、精度控制如何实现纳米级跨越?
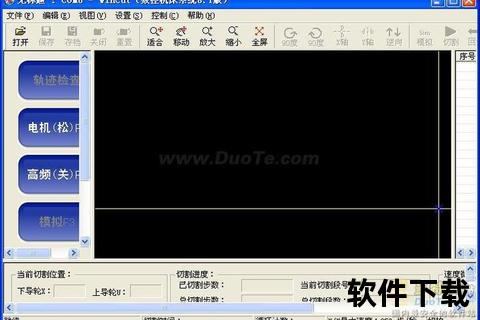
精度是线切割领域的核心指标。某医疗器械企业曾因0.02mm的切割误差导致钛合金骨钉报废,直接损失超20万元。而智能革新高效能线切割编程软件极速精准升级体验通过三重技术革新解决了这一难题:
第一,动态补偿算法。CAXA线切割V2版的轨迹偏移功能,可根据电极丝磨损实时调整进给量。测试数据显示,在连续切割高硬度钨钢时,系统将丝径损耗误差控制在±0.003mm内,比传统软件精度提升3倍。第二,4轴联动锥度控制。ESPRIT软件针对心脏支架模具的异形腔体,采用UV/XY双轮廓同步插补技术,使0.1mm薄壁结构的锥角误差从±0.5°降至±0.05°。第三,AI驱动的热变形预测。某数控系统开发商在CAM模块中集成机器学习模型,通过分析2000组历史加工数据,成功将热影响区收缩率预测准确度提升至98%,杜绝了微米级变形导致的密封件泄漏问题。
三、智能化转型怎样重构生产流程?
苏州某精密模具厂的案例极具代表性:该厂原有8名编程师,采用传统软件时人均日处理图纸仅2.5张。引入智能革新高效能线切割编程软件极速精准升级体验后,系统通过三大功能重构生产链——
图纸自动解析。软件可识别DWG、IGES等15种格式,甚至能将手机拍摄的手绘草图转化为矢量路径。在加工某品牌新能源汽车的曲面车灯模具时,设计部门提供的JPG格式概念图直接被转换为加工代码,节省了72%的前期准备时间。云端协同。华为5G工业模组与统达TwinCAD 3.2的结合,实现了跨厂区设备的状态监控。当杭州分厂的线切割机出现断丝预警时,深圳总部的工程师通过AR远程指导完成穿丝操作,故障响应时间从45分钟缩短至8分钟。生态互联。Mastercam 2025版已打通ERP系统,可根据订单优先级自动调度200台设备的加工队列,使该厂月产能从3000套跃升至8500套。
可操作性建议:
1. 优先选择跨平台兼容方案:如EdgeCAM支持Windows/Linux系统,并能与SolidWorks、CATIA等主流CAD软件无缝对接,避免数据转换损耗。
2. 注重AI模块的实际效能:要求厂商提供机器学习模型训练数据集规模(建议不低于5000组有效数据),并验证其在特定材料(如钛合金、碳化硅)上的预测准确度。
3. 建立数字化人才储备:统计显示,同时掌握CAE仿真与线切割编程的复合型工程师,可使设备利用率提升40%。建议企业每年投入至少15%的培训预算,重点培养参数优化、异常诊断等数字化技能。
这场由智能革新高效能线切割编程软件极速精准升级体验引领的技术革命,正在重塑制造业的价值链条。当传统的手动编程逐渐退出历史舞台,唯有主动拥抱智能化转型的企业,才能在精密制造的赛道上赢得未来。