智能工业转型遇瓶颈,PDPS如何破局?
当传统制造业向智能化转型时,一个尖锐的问题浮出水面:为什么投入大量资金引进机器人后,生产线的实际效率却提升有限? 这一问题背后,暴露出传统工业设计对复杂场景的模拟能力不足——例如设备干涉未被发现、工艺路径规划不合理、调试周期过长等。据统计,某汽车厂商曾因生产线布局失误导致机器人可达性不足,单次返工成本超千万元。而创新升级的PDPS仿真软件,正通过三维虚拟调试、工艺全链路优化等功能,强力驱动智能工业新浪潮,成为破解这一难题的关键工具。
1. 虚拟产线搭建,效率提升如何突破?
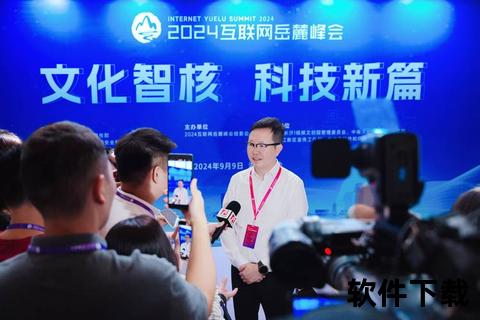
PDPS的核心突破在于将传统“物理试错”升级为“虚拟验证”。以某新能源汽车焊装线为例,工程师通过PDPS建立了包含200台机器人的数字化孪生模型,涵盖夹具定位、焊枪轨迹、节拍分析等全流程。在虚拟环境中,系统自动检测出12处机器人可达性不足和5处焊枪与车身的潜在干涉点,并生成优化路径。最终,该项目调试周期从8个月缩短至3个月,节省成本超40%。
更值得关注的是,PDPS的同步工艺树功能(如图1所示)实现了资源与工艺的实时映射。用户调整生产线布局时,系统自动更新工艺参数,避免了传统设计中“牵一发而动全身”的复杂性。某家电企业利用此功能,将产线改造成本降低了62%。
2. 复杂工艺验证,可靠性如何保障?
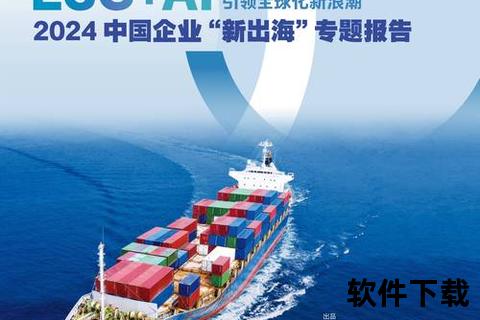
在高端制造领域,工艺容错率极低。PDPS通过多维度仿真引擎,将风险拦截在设计阶段。例如上海某汽车零部件供应商为宝马生产线设计夹具时,使用PDPS的碰撞检测功能,发现机器人末端执行器与夹具支撑柱存在3mm干涉风险。通过调整夹具角度和机器人姿态,避免了量产后的批次性质量问题。
PDPS的节拍平衡算法解决了多工位协同难题。某白车身焊装项目中,系统通过动态模拟焊点分配、机器人运动轨迹和物料流转,将单台车生产节拍从120秒优化至98秒,且设备利用率从75%提升至92%。这类案例证明,创新升级的PDPS仿真软件强力驱动智能工业新浪潮,正在重塑精密制造的标准。
3. 工业生态融合,技术边界如何拓展?
PDPS的创新不仅限于工具本身,更在于其开放式架构对工业生态的整合能力。通过OPC接口,PDPS可与西门子TIA Portal等PLC编程软件实时交互,实现“虚拟调试-物理执行”闭环。某发动机装配线项目中,工程师在PDPS中验证逻辑控制信号后,直接导出程序至现场设备,调试时间缩短70%。
更前沿的探索体现在与AI技术的结合。2025年,某头部车企计划将PDPS与端到端自动驾驶模型联动,模拟智能物流车的工厂内导航路径,预计使物料运输效率提升30%。这种跨领域的技术融合,标志着PDPS正从单一仿真工具进化为智能制造的中枢系统。
从工具到引擎:企业如何借力PDPS?
对于企业而言,引入PDPS需把握三个关键:
1. 分阶段实施:优先在焊装、总装等高复杂度工序试点,再逐步扩展至全流程;
2. 人才储备:联合培训机构开展PDPS认证课程,例如某职业院校已培养超500名仿真工程师,填补了行业技能缺口;
3. 数据闭环:建立虚拟调试与物理生产的反馈机制,持续优化模型精度。
创新升级的PDPS仿真软件强力驱动智能工业新浪潮,其价值不仅在于规避风险或降低成本,更在于为企业构建“设计-验证-生产”的一体化能力。当传统制造业仍在为调试失误付出代价时,先行者已通过PDPS将研发周期压缩、将质量隐患归零——这或许正是智能工业革命的真正起点。
--